The Human Factor in Workplace Safety: Understanding and Reducing the Risk
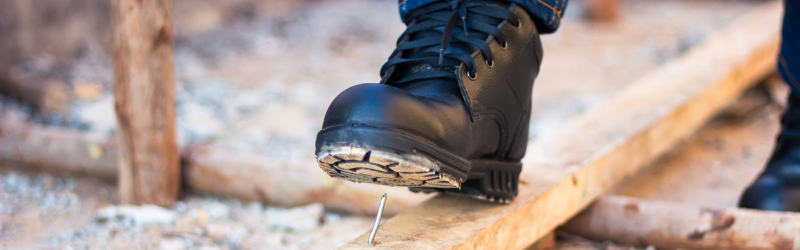
No matter how sophisticated your safety systems are, human slip ups remains one of the leading causes of workplace accidents. While systems and processes are essential for maintaining a safe environment, people are at the core of every workplace, and human error is inevitable. The good news is that, by understanding human behaviour, businesses can implement strategies to reduce errors and minimise the impact on workplace safety.
What is Human “Error” in the Workplace?
Human error can be broadly defined as an action or decision that unintentionally leads to an undesirable outcome, such as a workplace accident, injury, or near-miss. It encompasses a wide range of behaviours, including:
- Slip: A failure in performing an action, often due to inattention or distraction (e.g., accidentally pressing the wrong button).
- Lapse: Forgetting to complete an action (e.g., failing to secure a piece of machinery after use).
- Mistake: Incorrect decisions made based on incomplete or misunderstood information (e.g., using the wrong tool for a task due to misreading instructions).
- Breach: Deliberate deviation from established procedures, often because the worker believes the rules are unnecessary or inefficient.
Understanding these types of errors is key to implementing strategies that minimise their impact.
Contributing Factors to Human Error
Human error doesn’t occur in isolation. It is often the result of a combination of factors that create conditions where mistakes, slips, or lapses become more likely.
Here are some common contributors:
1. Fatigue
Long working hours, shift work, and physically demanding tasks can lead to fatigue, which could impair concentration, reaction times and decision-making.
2. Stress
Workplace pressures, tight deadlines, and challenging work conditions can increase stress levels, leading employees to make poor decisions or to overlook safety protocols.
3. Lack of Training
Employees who are not adequately trained are more likely to make errors. Whether it’s not knowing how to properly operate equipment or lacking awareness of safety procedures, insufficient training is a major risk factor.
4. Poor Communication
When communication breaks down, critical information may not be shared effectively. This can lead to misunderstandings, missed steps, or inconsistent application of safety measures.
5. Distraction
The modern workplace is filled with distractions – everything from noise and interruptions to mobile devices. Distraction can easily lead to slips or lapses in attention, particularly in tasks that require focus.
6. Complex Work Processes
Overly complicated systems, processes, or safety procedures can increase the likelihood of mistakes. Workers may skip steps, misunderstand procedures, or become overwhelmed by too much information.
Strategies to Reduce Human Error
While it’s impossible to completely eliminate human factors in the workplace, there are several effective strategies to reduce its occurrence and limit the risks associated with it:
1. Simplify Work Processes
Complex tasks and procedures can increase the chances of mistakes. One of the most effective ways to reduce human error is to simplify and streamline work processes wherever possible. This may include:
- Standardizing Procedures: Ensuring that processes are clear, consistent, and easy to follow.
- Automating Repetitive Tasks: Reducing the potential for manual errors by automating tasks where feasible.
2. Enhance Training Programs
Effective training plays a key role in minimising human factors that can lead to mistakes. Employees need to understand not only how to perform their tasks but why safety procedures are essential.
- Interactive Training: Incorporate hands-on training, role-playing, or simulation exercises to help workers retain knowledge better.
- Refresher Courses: Periodic refresher training can help reinforce critical safety practices and ensure that workers are up to date with the latest safety protocols.
3. Improve Communication
Clear and open communication is essential for reducing the likelihood of human mistakes. Ensure that workers are well-informed about safety practices, hazards, and any changes to work processes.
- Regular Safety Meetings: Schedule routine meetings to discuss safety concerns and reinforce procedures.
- Clear Documentation: Provide accessible and easy-to-understand documentation for workers, particularly regarding safety protocols and emergency procedures.
- Establish Feedback Loops: Create opportunities for employees to give feedback on safety procedures, equipment, and processes. This ensures that any issues or suggestions from those on the front lines are heard, leading to continuous improvement and early identification of potential risks.
4. Promote a Culture of Reporting Near Misses
Encourage employees to report near-miss incidents as these are often indicators of potential risks that, if left unaddressed, could lead to actual accidents.
- Blame Free Reporting Systems: Implement a system that allows workers to report near-misses or mistakes freely, without the worry of negative consequences. This encourages transparency and early intervention.
- Analyse and Act on Data: Use near-miss reports to identify patterns and address underlying issues before they escalate.
5. Address Fatigue and Stress
Fatigue and stress are significant contributors to human error. Employers should actively manage workloads, shift schedules, and offer support to reduce stress.
- Enforce Rest Periods: Ensure that workers have adequate rest between shifts and enforce mandatory breaks, especially during long or physically demanding work.
- Provide Stress Management Resources: Offer programs that support mental health and stress reduction, such as counselling, wellness programs, or flexible work arrangements.
6. Use Visual Cues and Alerts
Visual cues and alerts can help employees stay focused and aware of potential risks, reducing the likelihood of error.
- Signage and Labels: Use clear, color-coded signs to indicate hazards or important safety instructions.
- Warning Systems: Install audible or visual alerts to warn employees if they are about to perform an unsafe action (e.g., sensors that trigger if a machine is improperly operated).
7. Regular Audits and Safety Checks
Conduct regular audits of safety systems and work processes to ensure they remain effective and up to date.
- Safety Walks: Routine safety walks can identify potential risks and give employees an opportunity to voice any concerns.
- Incident Reviews: Analyse incidents and near-misses to understand the root causes and implement corrective actions to prevent recurrence.
Conclusion: A Proactive Approach to Human Error
Human behaviour will always be a part of any workplace, but by understanding the causes and proactively addressing the factors that contribute to it, businesses can greatly reduce the likelihood of accidents and improve overall safety performance. Whether it’s through simplifying processes, enhancing training, or fostering a culture of open communication, taking a proactive approach to managing human error is essential for creating a safer, more resilient workplace.
Talk to us today to see how Engage can help your organisation with this.