The Practical Application of NZ HSNO Regulations in a Large Landscaping Business
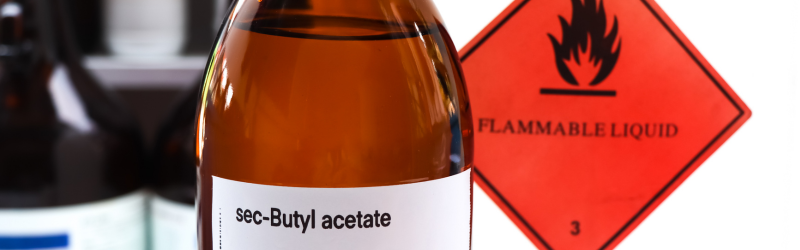
A Guide to Mitigating Risks and Avoiding Common Mistakes
by Gary Crook
Recently I was engaged to do a deep dive into the chemical handling practices of a large landscaping business that operates nationwide. This was not in response to an incident, but a peace of mind exercise requested by the Executive, a noteworthy decision from the business that takes its responsibility of safety very seriously.
What is HSNO?
The Hazardous Substances and New Organisms (HSNO) regulations in New Zealand are designed to ensure the safe use, storage, and transportation of hazardous substances. For large landscaping businesses, as in this case, adhering to these regulations is not only a legal requirement but also essential for the safety and wellbeing of employees and the environment. This article explores the practical application of HSNO regulations in a large landscaping business and highlights common risks and mistakes made by workers. This can be applied to many businesses in New Zealand, not just landscaping.
Understanding HSNO Regulations
HSNO regulations encompass a broad range of directives aimed at managing the lifecycle of hazardous substances, from manufacture and importation to use, storage, and disposal. In the context of a large landscaping business, these regulations cover various substances such as pesticides, herbicides, fertilizers, and fuel.
Decanting of Products
One of the common practices in landscaping businesses is the decanting of products from larger containers into smaller, more manageable ones. This process, while convenient, poses significant risks if not done correctly. Workers often make the mistake of not wearing appropriate personal protective equipment (PPE), leading to exposure to harmful substances. Additionally, using incorrect containers for decanting can result in chemical reactions or leaks.
Practice Tip: Always use containers that are compatible with the substance being decanted and ensure they are clearly labelled. Workers should be trained to wear suitable PPE, such as a respirator, gloves, and goggles, during the decanting process.
Incorrect Labelling
Correct labelling of hazardous substances is crucial for safety and compliance with HSNO regulations. However, it is not uncommon for workers to neglect this aspect, leading to confusion and potential mishandling of substances. Incorrect or missing labels can result in improper storage, usage, and even accidents.
Practice Tip: Implement a strict labelling protocol that includes details such as the substance’s name, hazard classification, risks, and handling instructions. Regular audits should be conducted to ensure compliance.
Incorrect Containers
Using inappropriate containers for storing hazardous substances is another common mistake in landscaping businesses. Containers that are not designed to hold specific chemicals can degrade or react with the contents, leading to leaks, spills, and contamination.
Practice Tip: Ensure that all containers are appropriate for the substances they hold. This includes checking compatibility and integrity regularly.
Poor Segregation and Storage of Substances
Proper segregation and storage of hazardous substances are vital to prevent chemical reactions and contamination. However, workers often store incompatible substances together or fail to follow storage guidelines, increasing the risk of accidents.
Practice Tip: Establish a designated storage area for hazardous substances, ensuring adequate segregation according to their hazard classifications. Provide clear signage and storage instructions to all employees.
Transportation of Substances in Vehicles
Transporting hazardous substances in vehicles requires adherence to specific guidelines to avoid spills and accidents. Workers sometimes overlook these guidelines, leading to unsafe transportation practices.
Practice Tip: Train employees on the correct procedures for transporting hazardous substances, including securing containers and following vehicle load limits. Regularly inspect vehicles to ensure they are equipped for safe transportation, spill control, and carriage of suitable spill kits.
Unintentional Spills
Spills are a common occurrence in landscaping businesses, often resulting from improper handling or storage of hazardous substances. Unintentional spills can lead to exposure to harmful chemicals and environmental contamination.
Practice Tip: Equip the workplace with spill kits and train employees on how to use them effectively. Establish an emergency response plan for handling spills and ensure quick and efficient cleanup.
Emergency Response
An effective emergency response plan is essential for managing incidents involving hazardous substances. However, many landscaping businesses lack such plans or have poorly executed ones, leading to inadequate handling of emergencies.
Practice Tip: Develop a comprehensive emergency response plan that includes procedures for different types of incidents. Conduct regular drills to ensure all employees are familiar with the plan and can respond promptly.
First Aid
First aid measures are critical in the event of exposure to hazardous substances. Workers may not always be aware of the specific first aid procedures required for different chemicals, leading to ineffective or delayed treatment.
Practice Tip: Provide training on first aid measures specific to the hazardous substances used in the business. Ensure that first aid kits are readily available and well-stocked.
Poor Safety Data Sheet (SDS) Controls
Safety Data Sheets (SDS) provide essential information on the handling, storage, and disposal of hazardous substances. Poor management of SDS can leave workers without critical information needed to work safely.
Practice Tip: Maintain an up-to-date SDS library accessible to all employees. Regularly review and update SDS to ensure they remain current. Before introducing a new substance into the workplace ensure that the SDS is reviewed and that all safe measures are put into practice and workers are trained in the new product.
Risk with a Lack of Training
A lack of proper training is one of the biggest risks in managing hazardous substances. Untrained workers are more likely to make mistakes that can lead to accidents and exposure to harmful chemicals.
Practice Tip: Implement a comprehensive training program that covers all aspects of hazardous substance management, including handling, storage, labelling, and emergency response. Regularly assess and update the training program to address new risks and regulations.
Conclusion
Adhering to HSNO regulations is essential for the safety and efficiency of a large landscaping business, or indeed any business that utilises hazardous substances in the workplace. By understanding common risks and mistakes and implementing best practices, businesses can create a safer working environment and ensure compliance with regulations. Continuous training and vigilance are key to preventing accidents and protecting workers from the dangers associated with hazardous substances.
Closing
No business is perfect, but that doesn’t mean that you can’t strive for perfection. The audit was completed with good results and with some recommendations for improvement. The business concerned have already stood up a working group to implement the recommendations, and preparation is underway for an emergency response exercise that will engage teams in the field, with of course the obligatory summer BBQ at the end.
Gary Crook is the founder of Phoenix Consulting Services; health, safety, and risk management specialists. With over thirty years’ experience in high-risk environments including NZ Police, deployments in the Middle East, and senior health and safety management roles in large high-risk NZ industries. Phoenix Consulting Services is available for safety management system reviews, auditing, investigations, emergency response training, and more.
Contact Phoenix Consulting Services;
P: 027 290 8527
Find out how Engage Solutions can help you manage your Hazardous Substance Register. Click here for a test drive today.
For further blog posts on Hazardous Substances click here