Safety Blind Spots
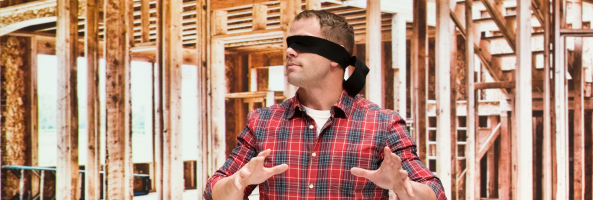
In health and safety, it’s easy to assume that established practices are always effective, but what if some of these well-intentioned measures are actually creating hidden risks? Over time, safety protocols can become rigid, and procedures designed to protect employees may inadvertently lead to complacency, underreporting, or a false sense of security. By blindly following “good practices” without questioning their actual real world effectiveness, organisations may be overlooking critical blind spots that can lead to dangerous consequences.
Below are some key blind spots that organisations may want to look at:
1. Overly Complex Safety Procedures
- The Issue: Many safety procedures are designed with the best intentions, but when they become overly complicated, employees may struggle to follow them. Workers may skip steps or find shortcuts to keep up with their workload.
- Potential Harm: Complex procedures can create a false sense of security, where it appears everything is safe on paper, but in reality, employees are not fully complying. This can increase the risk of incidents, as essential safety measures are bypassed.
- Example: A multi-step lockout/tagout process that is so cumbersome that workers bypass it to save time, leading to serious injuries.
2. Compliance-Driven Rather than Culture-Driven Approaches
- The Issue: Many organisations focus heavily on compliance with regulations and standards, ticking off boxes for audits, while neglecting the creation of a genuine safety culture. This can lead to a “bare minimum” mentality where the workforce is more concerned with passing inspections than adopting safety as a core value.
- Potential Harm: Safety becomes performative rather than ingrained in day-to-day activities. Workers may cut corners when they’re not being watched, leading to more frequent or severe incidents.
- Example: A company passes safety inspections but experience a rise in incidents because employees view safety as an external requirement rather than something they value internally.
3. Overconfidence in Technology
- The Issue: The rise of new technologies such as automation, AI-based monitoring systems, or protective equipment can give organisations a false sense of security. While these tools are valuable, over-reliance on them can lead to the neglect of human oversight and critical thinking.
- Potential Harm: Employees may become complacent, assuming that the technology will catch or prevent mistakes, and stop taking personal responsibility for their own safety. In cases where technology fails or is misapplied, the results can be disastrous.
- Example: Relying entirely on automated machinery inspections without periodic manual checks, leading to undetected wear and tear that eventually causes a major equipment failure.
4. Unintended Consequences of Safety Incentive Programs
- The Issue: Safety incentive programs—such as rewarding workers or teams for going a certain number of days without incidents—are often implemented to encourage safe behaviour. However, these programs can lead to underreporting of incidents and near misses, as employees may avoid reporting minor incidents to protect their rewards.
- Potential Harm: Underreporting prevents the organisation from addressing potential hazards early on, increasing the likelihood of major accidents down the line.
- Example: A team avoids reporting a near miss involving machinery because they don’t want to lose their safety bonus, and a more serious incident happens later.
5. Rigid Safety Protocols that Ignore Situational Flexibility
- The Issue: Some safety protocols are applied rigidly across all situations without room for adjustment. This one-size-fits-all approach can overlook the nuances of different tasks, environments, and personnel, leading to inefficiency or, worse, dangerous workarounds.
- Potential Harm: Workers may ignore or modify safety rules to fit the realities of their work environment, which can lead to unsafe practices becoming normalised.
- Example: A rigid rule requiring specific PPE for tasks that don’t always need it in certain conditions, leading workers to skip PPE use altogether – even when it is necessary – because they feel the rules are unreasonable.
6. Excessive Focus on Lagging Indicators
- The Issue: Many organisations focus on lagging indicators, such as the number of incidents or injuries, rather than leading indicators that measure potential risks before they result in incidents. This backward-looking approach may create a reactive, rather than proactive, safety culture.
- Potential Harm: By focusing too much on incident rates after the fact, organisations miss the opportunity to address systemic issues and near misses, allowing hazards to persist.
- Example: Focusing solely on reducing injury rates without examining near misses or unsafe conditions that could lead to future injuries.
7. Safety as a Siloed Function
- The Issue: In some organisations, safety is treated as a separate department or function rather than something integrated into all business operations. This can create a disconnect where safety is seen as someone else’s responsibility, leading to gaps in communication and collaboration.
- Potential Harm: Safety becomes isolated, and key operational decisions are made without fully considering their safety implications.
- Example: A manufacturing company schedules aggressive production targets without consulting the safety team, leading to rushed procedures and an increase in accidents.
8. Overemphasis on Paperwork and Documentation
- The Issue: In some safety programs, the emphasis is on maintaining detailed records, checklists, and documentation rather than fostering real engagement with safety practices. While documentation is important, when it becomes the primary focus, it can overshadow more meaningful safety efforts.
- Potential Harm: Workers and supervisors may see safety as a bureaucratic process, focusing on filling out forms rather than addressing real hazards in the workplace.
- Example: A company spends significant time on safety audits and inspections but fails to address root causes of recurring hazards.
9. Neglecting Psychological Safety
- The Issue: A blind spot in many safety programs is the failure to consider psychological safety—ensuring that workers feel comfortable speaking up about safety concerns without fear of retaliation. Without this, even the most robust safety system will miss key insights from the workforce.
- Potential Harm: Workers may withhold important information about hazards, unsafe behaviours, or near misses, leading to incidents that could have been prevented.
- Example: A worker notices a recurring hazard but doesn’t report it due to fear of being blamed, and an accident occurs later.
10. Safety Protocols that Stifle Innovation
- The Issue: While safety protocols are essential, overly restrictive rules can sometimes stifle innovation, making it difficult for employees to find more efficient or safer ways to do their jobs. An excessive focus on compliance can limit creative problem-solving.
- Potential Harm: Employees may feel trapped by the “system” and feel unable to suggest or implement improvements, leading to inefficiencies or even frustration-driven unsafe behaviour.
- Example: Employees aren’t allowed to modify outdated equipment to make it safer because it’s not in the official safety guidelines, despite the obvious benefits of doing so.
Recognizing and addressing these blind spots is essential for creating a truly effective health and safety culture. While established practices are important, they should never be followed blindly. By regularly reviewing and refining your protocols, encouraging open communication, and remaining adaptable to new challenges, organisations can ensure that their safety measures evolve with the times and continue to protect their employees.
For more information on how Engage can help you with this, contact us today…..