Contextual Data in Safety Decisions
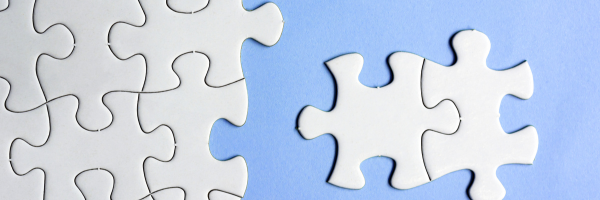
The Role of Contextual Data in Safety Decisions
When it comes to workplace safety, data is invaluable. Metrics such as incident rates, near-miss reports, and compliance checklists can provide essential insights into safety performance. However, relying solely on these numbers can lead to a one-dimensional view of safety. This is where contextual data comes in to play. By incorporating additional, situational information, companies can make smarter, more informed safety decisions that address the complexities of real-world operations.
What Exactly Is Contextual Data?
Contextual data refers to a broader set of factors that influence safety beyond standard metrics. It includes information about the environment, tasks, workforce conditions, and even cultural or behavioural factors. This data enriches safety analytics by adding depth and clarity, helping companies understand why certain risks exist and how they can be effectively mitigated.
Examples include:
• Task-specific factors: Complexity, duration, and tools or equipment used.
• Environmental conditions: Weather, lighting, noise levels, and temperature.
• Workforce variables: Worker fatigue, experience levels, and team dynamics.
• Operational context: Production pressures, scheduling conflicts, or high-risk timelines.
How Does It Help Your Safety Decisions?
1. Uncovering Hidden Risks
• Standard metrics like injury rates often fail to capture the nuanced conditions that lead to incidents. For example, data might show an increase in slips and falls, but contextual information about recent rainfall or poor lighting reveals the root cause.
• By analyzing contextual factors, companies can identify risks that are not immediately apparent in incident reports.
2. Improving Root Cause Analysis
• Contextual data provides a richer foundation for investigating incidents or near misses. Understanding the task environment, worker behavior, and external influences helps companies pinpoint the true cause of an event and implement targeted solutions.
3. Tailoring Safety Interventions
• Generic safety measures often fail to address the specific needs of different tasks or work environments. Contextual data allows for customized safety protocols, such as issuing heat-resistant PPE for workers in high-temperature environments or scheduling frequent breaks for teams working under high production pressure.
4. Enhancing Predictive Capabilities
• Advanced analytics tools can use contextual data to predict potential risks. For example, analyzing trends in worker fatigue, task complexity, and environmental conditions can help forecast when and where incidents are most likely to occur.
5. Building Worker Trust and Engagement
• Incorporating contextual data demonstrates that the company values worker input and understands the challenges they face. This fosters a culture of trust, where workers feel their concerns are heard and addressed.
Practical Steps to Integrate Contextual Data
1. Gather Comprehensive Inputs
• Use multiple data sources, including hazard observation reports, environmental monitoring, worker surveys, and real-time sensors, to collect contextual information.
2. Leverage Technology
• Invest in safety management software (like Engage!) that can integrate contextual data. Tools like environmental sensors and digital checklists provide real-time insights into on-the-ground conditions.
3. Train Workers and Supervisors
• Teach employees and supervisors to recognize and document contextual factors in hazard and incident reports. This ensures data collection is consistent and accurate.
4. Combine Contextual and Traditional Metrics
• Contextual data should complement, not replace, traditional safety metrics. Use it to provide additional layers of insight into lagging and leading indicators.
5. Analyze and Act
• Regularly review contextual data alongside standard metrics to identify patterns and opportunities for improvement. Use these insights to implement tailored interventions and monitor their effectiveness.
Case Study: Contextual Data in Action
Scenario:
A manufacturing plant experienced an increase in minor hand injuries despite robust safety training and PPE compliance. Initial analysis of incident data did not reveal a clear trend.
Contextual Insights:
By reviewing contextual data, the safety team discovered:
• Workers were handling materials in a new production area with dim lighting.
• The pace of work had increased to meet an urgent delivery deadline.
• Many workers assigned to the task were new and lacked experience.
Outcome:
The company addressed these factors by improving lighting, adjusting production schedules to reduce time pressure, and pairing new workers with experienced ones. These changes led to a significant reduction in hand injuries.
Contextual data is the missing piece in many companies’ safety analytics frameworks. By understanding the “why” behind safety risks, companies can make more informed decisions, tailor interventions, and create safer workplaces. While traditional metrics remain important, integrating contextual data provides the depth and clarity needed to move beyond the illusion of safety and address real-world challenges.
At Engage, we believe in empowering organizations to harness the power of contextual data in safety decisions. Let us help you build a data-driven safety culture that keeps your workforce safe, engaged, and productive.
Contact us today to learn more