The Importance of Maintenance in Manufacturing
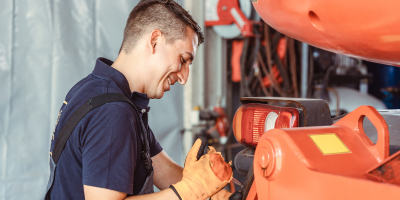
In the fast-paced world of manufacturing, machinery is the backbone of production. Ensuring that machinery operates smoothly and efficiently is crucial for maintaining not just productivity but also safety, and profitability. Proper machinery maintenance not only extends the lifespan of equipment; it also significantly reduces the risk of accidents and downtime. In this post, we will explore the importance of machinery maintenance and provide best practices for keeping your manufacturing operations running smoothly.
Why Machinery Maintenance is Crucial
1. Enhanced Safety
• Prevent Accidents: Regular maintenance helps identify and fix potential hazards before they cause accidents, protecting workers from injury.
• Compliance with Regulations: Adhering to maintenance schedules ensures compliance with safety regulations and standards, avoiding legal issues and fines.
2. Increased Equipment Lifespan
• Proactive Care: Routine maintenance prevents excessive wear and tear, helping machinery last longer and perform better.
• Cost Savings: Investing in maintenance reduces the need for costly repairs and replacements, leading to long-term cost savings.
3. Improved Productivity
• Minimized Downtime: Regularly serviced machinery is less likely to break down, ensuring uninterrupted production and meeting deadlines.
• Optimal Performance: Well-maintained equipment operates at peak efficiency, enhancing overall productivity and product quality.
4. Reduced Operational Costs
• Energy Efficiency: Properly maintained machines consume less energy, reducing operational costs and environmental impact.
• Predictable Expenses: Scheduled maintenance allows for better budgeting and financial planning, avoiding unexpected repair costs.
Best Practices for Machinery Maintenance
1. Develop a Maintenance Schedule
• Regular Inspections: Create a schedule for routine inspections and servicing based on manufacturer recommendations and equipment usage.
• Preventive Maintenance: Implement preventive maintenance programs to address issues before they escalate, including cleaning, lubrication, and parts replacement.
2. Train Your Team
• Skilled Personnel: Ensure that maintenance tasks are performed by trained and qualified personnel who understand the machinery and its requirements.
• Ongoing Education: Provide ongoing training and education to keep the team updated on the latest maintenance techniques and safety protocols.
3. Use Technology
• Monitoring Systems: Employ predictive maintenance technologies, such as sensors and monitoring systems, to track equipment performance and predict potential failures.
• Maintenance Software: Utilise maintenance management software (included as part of Engage!) to schedule tasks and track maintenance history.
4. Keep Detailed Records
• Maintenance Logs: Maintain detailed records of all maintenance activities, including dates, tasks performed, and parts replaced, to identify patterns and plan future maintenance.
• Compliance Documentation: Ensure that all maintenance records comply with industry regulations and standards for easy reference during audits and inspections.
5. Focus on Critical Machinery
• Prioritise Key Equipment: Identify and prioritise the maintenance of critical machinery that has the greatest impact on production and safety.
• Risk Assessment: Conduct risk assessments to determine which machines are most likely to fail and focus maintenance efforts accordingly.
6. Regular Audits and Reviews
• Performance Audits: Regularly audit the performance of your maintenance program to identify areas for improvement and ensure that it meets the needs of your operations.
• Continuous Improvement: Foster a culture of continuous improvement by encouraging feedback from maintenance personnel and operators.
Effective machinery maintenance is a cornerstone of successful manufacturing operations. By implementing a robust maintenance program, you can enhance safety, extend equipment lifespan, improve productivity, and reduce operational costs. Investing in regular maintenance not only protects your workforce and equipment but also contributes to the overall efficiency and profitability of your manufacturing business.
At Engage, we understand the critical role that machinery maintenance plays in manufacturing. Contact us today to learn how our comprehensive health and safety solution can support your maintenance program and ensure a safe, efficient, and productive work environment.